SustainAbility: interconnessi nella sostenibilità – Paper n. 3- tratto da Green Logistics
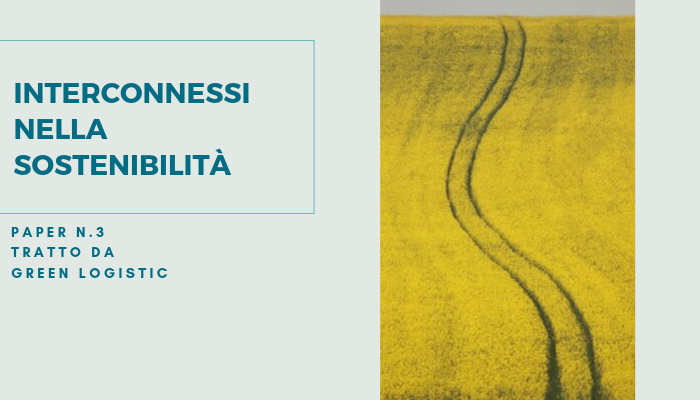
In questo articolo vedremo quali elementi misurare per tenere sotto controllo l’efficienza nei trasporti. Nei paesi più sviluppati il trasporto su gomma è la modalità di trasporto merci dominante. L’efficienza nel trasporto merci è quindi una delle maggiori determinanti dell’impatto ambientale operato dalla logistica: se tutti i camion viaggiassero sempre a pieno carico, l’impatto ambientale si ridurrebbe in maniera significativa.
Alcuni fatti:
- Approssimativamente il 25% dei km percorsi dai camion europei è per viaggi a vuoto;
- Il trasporto di cibo occupa solo il 52% di ogni carico completo (il resto è aria);
- Un camion da 44 tonnellate capace di trasportare un carico da 29 tonnellate, trasporta in media 17,6 tonnellate quando viaggia a carichi completi e 12,7 se accetta corse a vuoto.
Aumentare il fattore di carico è un obiettivo primario per le imprese di trasporti poiché conduce a risultati economici e benefici ambientali.
Accrescere l’efficienza nei carichi, infatti, se da un lato accresce il margine medio per viaggio, parallelamente riduce il traffico stradale e il congestionamento.
Ton-KM per veicolo per anno
Questo indicatore è essenzialmente una misura di produttività ed è ampiamente utilizzato; non è un indicatore utile per tenere conto della sostenibilità e dell’impatto ambientale del trasporto gommato, non fornisce indicazioni sulla proporzione del veicolo effettivamente utilizzato.
Weight – Based Lading
Questo indicatore è esclusivamente legato al peso del carico ed è generalmente espresso come “l’effettiva merce movimentata al massimo tonellaggio per km raggiungibile se i veicoli, fossero sempre caricati alla loro massima capacità”.
Ci fornisce un dato incompleto, basti pensare come tale indicatore si sia ridotto in media in Inghilterra dal 63% del 1990 al 57% del 2007, non già per una maggiore efficienza aziendale, quanto per un aumento della capacità di carico dei camion, passati da 38 tonnellate a 41 e poi a 44 tonnellate nel 2001. Al contempo il fattore medio di carico si è ridotto, tale aspetto è connesso alla introduzione di materiali meno densi, si trasporta meno legno e metallo e sempre più plastica e imballaggi. Ciò accresce la cubatura del trasportato riducendone il peso, per tale ragione il peso del carico sta divenendo un indicatore poco significativo, mentre cominciano ad essere utilizzati indicatori legati ai volumi trasportati, più idonei per analizzare le performance di trasporto di sostanza a bassa densità.
Vehicle fill rate
Traducibile come “tasso di riempimento del veicolo” è un indicatore dato dalla percentuale di spazio occupato da un carico o dalla proporzione dell’area del pianale di carico occupato.
In caso di carichi normalizzati all’unità, grazie a pallets o all’uso delle gabbie, il numero effettivo di unità trasportate può essere diviso per il massimo numero di unità trasportabili per determinarne la percentuale di riempimento.
Viaggi a vuoto
Questo indicatore analizza la proporzione di veicoli che percorre km a vuoto. Percorrere tratte a vuoto è l’inevitabile conseguenza dell’unidirezionalità delle consegne, dai luoghi di produzione a quelli di commercializzazione, ad esempio, e la difficoltà di bilanciare il flusso di merce nelle due opposte direzioni. Un problema molto sentito in Italia, dove il Sud produce per i mercati di sbocco del Nord e i mezzi tornano vuoti al Sud una volta completato il lavoro.
All’interno dell’Unione Europea la media dei viaggi a vuoto è del 27% anche se varia in modo considerevole da Paese a Paese sulla base di fenomeni connessi alla morfologia dei diversi territori e all’economia degli stessi. Il livello di viaggi a vuoto tende ad essere inversamente proporzionale alla lunghezza del tragitto, poiché a tragitti più lunghi corrisponde un maggiore incentivo nel trovare un viaggio di ritorno che ammortizzi i costi. I viaggi a vuoto non sono solo una perdita economica, ma anche una penalità ambientale rilevante.
Vi sono ovviamente molteplici ragioni che costringono gli operatori logistici ad effettuare viaggi a vuoto. Possiamo notare nel grafico 1 che segue le principali cause di tale inefficienza.
- Vincoli di mercato sono associati con i percorsi della merce e con la fluttuazione dei volumi nel tempo.
- Vincoli regolatori determinano la dimensione e il peso dei veicoli, i tempi di consegna così come gli aspetti di salute e di sicurezza nel trasporto, nel carico e scarico dei beni trasportati.
- I vincoli inter-funzionali sono quelli imposti alla gestione dei trasporti da altri dipartimenti aziendali;
- Vincoli infrastrutturali sono legati alla capacità fisica del network dei trasporti così come alla capacità di stoccaggio ad inizio e fine trasporto.
- Vincoli connessi all’equipaggiamento risultano dall’incompatibilità di veicoli, sistemi di caricamento e trasporto.
Vi sono quindi motivazioni perfettamente razionali che fanno propendere per una efficienza nel trasporto più bassa. Il risultato di tutti i costi legati alla logistica potrebbe ridursi con un uso sub-ottimale del trasporto, a svantaggio dei benefici ambientali che derivano da un uso più efficiente dello stesso. Bassi livelli di magazzino, uso ottimale degli spazi di stoccaggio e massimizzazione della produttività del personale addetto alla baia di carico potrebbero pesare di più dell’inefficienza derivante dai viaggi a vuoto
Fluttuazioni della domanda
I volumi di vendita possono variare ampiamente su base giornaliera, settimanale, mensile e stagionale in modo ciclico. La Figura 2, ad esempio, illustra il flusso giornaliero medio di generi alimentari nella catena di approvvigionamento alimentare del Regno Unito. La capacità del veicolo è spesso pianificata per soddisfare la domanda di punta, lasciando altre volte inevitabilmente in eccedenza (surplus) la capacità della flotta. Le aziende sono soggette a pronunciate e prevedibili fluttuazioni stagionali che possono assumere veicoli aggiuntivi o esternalizzare più del loro trasporto nei periodi di punta. È più difficile adottare la loro strategia dove vi sono variazioni ampie e imprevedibili nella domanda di trasporto da giorno a giorno.
Figura 2 Fluttuazione della domanda giornaliera nel settore alimentare: percentuale in volume
Fonte: Dipartimento per i trasporti britannico (2007).
Se i gestori dei trasporti e i vettori possono ricevere avvisi più avanzati della domanda futura possono pianificare molto di più l’uso della capacità del veicolo in modo efficace. Uno degli obiettivi chiave del Collaborative Transportation Managment (CTM) deve coinvolgere i manager responsabili dell’operazione di trasporto in una fase precedente del processo logistico (Browning e White, 2000). Creando un “orizzonte di pianificazione esteso” di alcuni vettori sono stati in grado di aumentare l’utilizzo delle loro flotte di camion regionali negli Stati Uniti tra il 10 e il 42 per cento, principalmente a causa del miglioramento manageriale dei responsabili (Esper e Williams, 2003).
NDDS
Il Nominated Day Delivery System (NDDS) è una procedura che aiuta le aziende ad ottenere livelli molto più elevati di efficienza dei trasporti facendo sì che i clienti aderiscano ad un ordine ed ai tempi di consegna. Le aziende sono informate che un veicolo visiterà la propria area in un giorno “definito e tassativo” e che per ricevere una consegna in quel giorno devono presentare il loro ordine d’acquisto con un certo anticipo.
Concentrando le consegne di determinate zone in particolari giorni della settimana, i fornitori possono raggiungere livelli più elevati di consolidamento del carico, calo di densità e utilizzo del veicolo. Questa pratica è tuttavia entrata in contrasto con le esigenze dei responsabili delle vendite poiché questi compromettono lo standard del servizio al cliente e questa pratica può indebolire la posizione competitiva dell’azienda rispetto alla concorrenza.
Alcune fluttuazioni della domanda sono indotte artificialmente da alcunie prassi: l’attività promozionale, ad esempio, destabilizza il flusso di merci, rendendo più difficile la gestione della capacità di trasporto ad un livello uniformemente elevato. La normale pratica di pagare le bollette alla fine del mese e dare obiettivi mensili agli addetti alle vendite provoca anche il picco dei volumi di trasporto all’inizio del mese. La capacità del veicolo fornita per soddisfare questo picco è spesso sottoutilizzata più avanti nel mese. Rilassare il ciclo di pagamento mensile e passare a un sistema di “credito continuativo”, in cui i clienti hanno ancora lo stesso tempo di pagamento, ma piuttosto dalla data dell’ordine rispetto all’inizio di un mese del calendario, può migliorare significativamente l’utilizzo del veicolo. È stato suggerito, ad esempio, che dare un credito continuativo potrebbe ridurre significativamente i costi della catena di approvvigionamento e gli impatti ambientali nella nell’industria chimica Europea (McKinnon, 2004).
Mancanza di conoscenza delle opportunità di caricamento
Se gli operatori del trasporto detenessero una perfetta conoscenza di tutti i carichi disponibili per consegna in tutte le località e in qualsiasi momento sarebbero in grado di ottenere livelli molto più elevati di carico del veicolo su entrambi i viaggi di andata e ritorno. Molte opportunità di abbinamento del carico mancano a causa dell’assente comunicazione tra potenziali vettori e spedizionieri.
Tradizionalmente questo ruolo è stato svolto degli intermediari nel mercato del trasporto merci, come spedizionieri e broker, fungendo da stanze di compensazione per informazioni su carichi e veicoli disponibili. Tali professionisti si affidavano alla conoscenza del mercato, reti personali e telefono per concordare accordi tra spedizionieri e corrieri. Con l’avvento di Internet è emersa una nuova generazione di scambi di merci, fornendo gare d’appalto abilitate al web, aste online e bacheche per i servizi di trasporto di merci su strada (Sarkis, Meade e Talluri, 2000; Lewis, 2001). Questo ha notevolmente migliorato le opportunità di abbinamento dei carichi con la capacità del veicolo, in particolare sui trasporti da effettuare per il viaggio di ritorno.
Squilibri geografici nel flusso del traffico
A differenza dei passeggeri, che normalmente effettuano viaggi di ritorno, quasi tutte le merci si muovono versa una sola direzione. Le quantità di merci spostate tra coppie di Paesi e le regioni sono raramente equilibrati. Anche se c’è parità nel livello commerciale in termini monetari, gli importi fisici delle merci spostati in direzioni opposte può essere abbastanza diverso. È stato stimato che nel 2003, 130.000 camion viaggiarono vuoti tra Scozia e Inghilterra, riflettendo un rapporto di 1: 1,31 nel tonnellaggio di merci trasportate su strada tra i due Paesi.
Il modo principale in cui i vettori affrontano tali squilibri di traffico è adottando una pratica chiamata “triangolazione”. Invece di guidare veicoli sulle rotte bilaterali dalla A alla B, le inviano su viaggi interregionali più complessi (ad es. da A a B da A a C), che possono consentire loro di sfruttare gli squilibri del traffico in direzioni opposte lungo il percorso e quindi aumentano il fattore di carico medio nel viaggio nel suo insieme.
Consegna Just-in-time (JIT)
L’obiettivo del JIT è quello di ottenere un flusso continuo di materiali attraverso la catena di approvvigionamento, nel tentativo di ridurre al minimo le scorte. La sincronizzazione dei trasporti con il processo di produzione e la criticità temporale delle consegne JIT, spesso comportano consegne in tempi brevi e in piccole quantità. In queste circostanze, l’utilizzo efficiente della capacità di trasporto può essere sacrificato per un inventario inferiore e più una produzione più flessibile. Le politiche a basso inventario e la consegna JIT sono ormai la norma in molti settori industriali. Non sorprende quindi che JIT riceva gran parte della colpa per il sottoutilizzo di camion e conseguenti crescite del traffico merci e danno per l’ambiente.
Gli effetti negativi del JIT sull’efficienza dei trasporti possono essere attenuate grazie a razionalizzazioni del sistema logistico in entrata. Ad esempio, alcune case automobilistiche, come Nissan (DETR, 1998a), hanno impiegato un servizio di fornitori logistico per raccogliere componenti dai fornitori e consolidarli presso un hub prima della consegna a JIT direttamente alla linea di produzione. Il raggruppamento di stabilimenti dei fornitori, centri commerciali e magazzini intorno a automobili e computer e gli impianti di assemblaggio hanno inoltre ridotto al minimo le distanze di consegna JIT. Nel settore del commercio al dettaglio, le pressioni equivalenti di “risposta rapida”, hanno portato all’inserimento di un ulteriore livello di “consolidamento primario” tra la fabbrica e il centro di distribuzione in cui si trovano i prodotti di diversi produttori aggregati in carichi di dimensioni ragionevoli.
Mancanza di coordinamento interfunzionale
L’uso scarso del camion può essere, in molte imprese una conseguenza della struttura dipartimentale del “silo” che inibisce la comunicazione e il coordinamento tra le funzioni. Mancanza di collegamento tra gli acquisti e il personale logistico si traduce spesso in potenziali opportunità di mancanza del carico sulla via di ritorno, mentre il personale di vendita può assumere impegni nei confronti dei clienti che comportano la consegna di merci in veicoli scarsamente caricati. Questo problema può essere alleviato dall’applicazione di buone pratiche commerciali, coinvolgendo la sostituzione dei silos con una più efficace gestione interfunzionale di processi fondamentali, uno dei quali è l’adempimento degli ordini dei clienti (Christopher, 2005).
Priorità data alle consegne in uscita
Le aziende danno naturalmente priorità alla distribuzione dei loro prodotti ai clienti e sono riluttanti a ricaricare un veicolo quando hanno la paura che potrebbe non tornare in tempo per essere caricato con la successiva spedizione in uscita. Questa remora è stata identificata come uno dei principali vincoli al backloading (carico di ritorno), in particolare laddove i programmi di consegna non sono affidabili (McKinnone Ge, 2006). Il modo principale per affrontare questa preoccupazione è migliorare l’affidabilità e la “visibilità” delle operazioni di trasporto merci su strada in modo da offrire ai gestori maggiore fiducia nei programmi di distribuzione.
Mancanza di cooperazione attraverso la catena di approvvigionamento
C’è un limite a quanto una singola azienda possa fare per migliorare da sola l’utilizzo dei veicoli che trasportano i prodotti. Le decisioni delle società a monte e a valle della catena di approvvigionamento possono limitare le opportunità per migliorare i fattori di carico e ridurre i chilometri dei camion. Se i partner della catena di approvvigionamento sono pronti a collaborare, possono essere realizzati livelli di utilizzo molto più elevati: si può fare una distinzione tra collaborazione orizzontale; dove le aziende allo stesso livello della catena di approvvigionamento lavorano insieme, e la collaborazione verticale; che implica un’azione collettiva attraverso il trading partner a diversi livelli in una catena di approvvigionamento. In entrambi i casi, le logistiche dei fornitori di servizi possono svolgere un ruolo chiave.
Collaborazione orizzontale
Newing (2008) ha stimato che se due imprese concorrenti si fondono, le loro operazioni logistiche e le consegne dei veicoli possono tagliare (insieme) i loro costi di trasporto del 15-20%. Tale società incrociata / e le collaborazioni all’interno dello stesso settore, possono assumere varie forme.
Nel settore petrolifero, ad esempio, gli accordi di scambio tra compagnie petrolifere consentono alle raffinerie di fornire tutte le stazioni di rifornimento in un’area locale indipendentemente dal marchio, massimizzando densità di caduta e riduzione delle distanze vuote di backhaul. Nel settore dei beni di consumo (FMCG) in rapido movimento ci sono esempi di imprese che fondono le loro operazioni logistiche in una struttura di distribuzione condivisa e combinano i carichi del veicolo. Ciò è ben esemplificato dal consolidamento di prodotti Unilever e Kimberly-Clark per il mercato al dettaglio olandese al centro di distribuzione gestito per loro da Kuehne e Nagel in Raamsdonksveer (Cruijssen, 2007). Come risultato di questa collaborazione le aziende sono state in grado di ridurre i costi logistici del 12-15% rispondendo alle richieste dei rivenditori e ottenendo consegne in modo più rapido e frequente. Nel Regno Unito Nestlé e United Biscuits, che sono concorrenti nei mercati dei biscotti e della pasticceria, hanno lavorato insieme per tagliare le corse dei camion vuoti tra lo Yorkshire e le Midlands (Clements, 2008).Questo fa parte di una più ampia iniziativa dell’industria alimentare che coinvolge “37 aziende leader del Regno Unito nel settore alimentare e dei beni di consumo che hanno rimosso l’equivalente di 53 milioni di miglia di viaggio dalle strade del Regno Unito ” (IGD, 2008a).
Collaborazione verticale
Esistono anche diversi tipi di collaborazione verticale. Uno dei più comuni è la raccolta di forniture in entrata da parte di un veicolo di ritorno dalla consegna. Questa è ormai una pratica comune nel settore della drogheria al dettaglio dove i camion di ritorno dai supermercati fanno un viaggio triangolare per raccogliere ordini dai fornitori e trasportarli al centro di distribuzione. Questa forma di “raccolta dei fornitori” riduce sostanzialmente il chilometraggio a vuoto (DfT,2005a). Una variante di questo schema, noto come “consegna successiva”, comporta veicoli dei fornitori che consegnano ai negozi del rivenditore durante il loro ritorno dal centro di distribuzione alla fabbrica. Attraverso queste forme di collaborazione verticale con fornitori a monte, la catena di supermercati britannica Tesco è stata in grado di risparmiare circa 3 milioni di viaggi all’anno (DETR, 1998b).
Laddove i partner commerciali nel canale verticale adottano un inventario fornito dal venditore (VMI), il fornitore assume il controllo del processo di rifornimento e può quindi spostare gradualmente il movimento dei prodotti che ottimizza l’uso della capacità del veicolo. Disney, Potter e Gardner (2003) hanno utilizzato la modellazione di simulazione per dimostrare i vantaggi potenziali del trasporto del VMI rispetto a una “catena di approvvigionamento tradizionale”. Anche se il VMI può comportare una maggiore quantità di inventario presso la sede del cliente in genere verrebbero addebitati solo per i materiali di consumo quando sono effettivamente utilizzati (o “annullati”).
Una maggiore efficienza di trasporto può essere raggiunta nella distribuzione locale alle case e ai locali commerciali attraverso l’uso di “consegne automatiche”. Quando i clienti installano una cassetta di ricezione, il corriere può esercitare un controllo molto maggiore sul programma di consegna, migliorando l’efficienza del carico e del percorso del veicolo eliminando virtualmente il rischio di una consegna fallita. Una ricerca a Helsinki ha suggerito che l’uso di cassette di accoglienza può ridurre i costi di trasporto, le distanze di consegna e le esternalità correlate di ben il 40% (Punakivi, Yrjölä e Holmström, 2001). La collaborazione verticale nel campo della logistica inversa può massimizzare il ritorno del flusso di rifiuti, prodotti danneggiati e indesiderati su backhaul. Ciò offre un notevole potenziale per ridurre il funzionamento a vuoto e farebbe contribuire al 20–40% dei risparmi sui costi di trasporto che potrebbero essere raggiunti se i rivenditori dovessero razionalizzare il flusso inverso per i prodotti resi provenienti da negozi (Cranfield University, Sheffield Hallam Universitye CILT, 2004). La logistica inversa è l’obiettivo principale del capitolo 11.
Inaffidabilità nei programmi logistici
Pianificare il backhaul e le rotte più complesse, che spesso richiedono di massimizzare il carico del veicolo, implica che i gestori debbano avere fiducia nella programmazione. Fortunatamente, molta congestione del traffico è regolare e prevedibile. Più problematici sono gli imprevisti, gli incidenti di traffico casuali, come i maggiori incidenti e lavori stradali, che aiutano a migliorare la variabilità dei tempi di transito. È stato stimato che nel Regno Unito circa il 24% delle consegne delle merci venga ritardato e circa il 34% di questi ritardi è attribuito principalmente alla congestione del traffico (McKinnon, 2009). Le deviazioni dal programma sono anche dovute ad una serie di altri fattori, tra cui la congestione presso i centri di distribuzione, guasti ai veicoli e assenteismo del personale.
I progressi nell’IT consentono il tracciamento di camion, fornendo un preavviso per ritardi e consentendo ai gestori di flotte di ripianificare i percorsi in tempo reale mentre il veicolo è in viaggio per ridurre al minimo l’impatto della congestione. La riprogrammazione delle consegne in serata e in nottata può anche ridurre la variabilità del tempo di transito. Per ritardi originati in fabbriche, magazzini e negozi, sono spesso richieste alcune re-ingegnerizzazioni di processi interni e, in caso di congestione backdoor, la fornitura di capacità aggiuntiva. Aumentando il rapporto tra trattori e rimorchi in una flotta di veicoli articolati (cioè il “rapporto di articolazione”) può disaccoppiare l’operazione di trasporto dall’attività di carico / scarico, riducendo il rischio di ritardi in entrata che limitano il fattore di carico in uscita.
Progettazione di attrezzature per imballaggio e movimentazione
La natura del packaging influenza l’efficienza con cui lo spazio è utilizzato in edifici e veicoli lungo la catena di approvvigionamento. Forma, dimensione e impilabilità possono comportare uno scarso utilizzo della capacità del veicolo. Le attrezzature per la movimentazione possono essere modificate per consentire una manipolazione conveniente nonché un uso efficiente della capacità di trasporto e di stoccaggio. Un fabbricante di cibo francese, ad esempio, è stato in grado di migliorare il riempimento del veicolo del 35–41% imballando gli ordini in moduli di varie altezze (Università di San Gallo, 2000). La quantità totale di imballaggi sui prodotti può anche essere ridotta, spesso senza aumentare i livelli di danno lungo la catena di approvvigionamento. La catena di supermercati britannica Asda, ad esempio, punta a ridurre gli imballaggi della propria gamma di prodotti con etichetta propria del 25% (IGD, 2008b). Il packaging può anche essere riprogettato per migliorare la sua “efficienza nello spazio”. Gli sforzi sono stati fatti, ad esempio, per sostituire le lattine rotonde con quelle quadrate per ridurre i requisiti di spazio del 20% in veicoli, magazzini e negozi (Sonneveld, 2000).
Incompatibilità di veicoli e prodotti
Alcuni veicoli sono limitati a trasportare solo determinate merci, limitando i tipi di carico che possono raccogliere su un viaggio di ritorno.
Non è possibile, per esempio, trasportare carichi pallettizzati su una nave cisterna o merci refrigerate in un rimorchio senza controllo della temperatura.
Ciò limita la corrispondenza dei carichi con la capacità disponibile del veicolo su percorsi particolari. È stato possibile riprogettare i veicoli per adattarsi a un mix più ampio di prodotti, spesso nello stesso viaggio. La compartimentazione dei camion ha permesso ai rivenditori di generi alimentari e ai loro appaltatori di combinare il movimento di prodotti a diverse temperature in un unico viaggio. Questa forma di “distribuzione composita”, ad esempio, ha consentito al rivenditore britannico Safeway di ridurre il numero medio di viaggi in auto necessari per la consegna in 1000 casi da cinque nel 1985 a uno nel 1995 (Freight Transport Association,1995).
Limitazioni di dimensioni e peso del veicolo
Possono esservi restrizioni legali su pesi e dimensioni del peso del veicolo e ciò può portare ad una sottoutilizzata capacità di carico volumetrico (McKinnon, 2005). Poiché i limiti di peso sono stati aumentati di un margine maggiore rispetto ai limiti di dimensione negli ultimi decenni, in un periodo in cui la densità media del trasporto merci è in calo, una percentuale più elevata di carichi è ora vincolato al volume rispetto al peso obbligato. Questo è chiaramente illustrato nel Regno Unito, dove poco più del doppio dei carichi trasportati dai camion con pesi lordi di oltre 38 tonnellate sono limitati dal volume in quanto limitati dal peso (Figura 3).
Aumentare la dimensione massima dei camion può quindi consentire alle aziende di consolidare i carichi, ottenendo un maggiore riempimento del veicolo e diminuendo i chilometri del camion. È possibile ottenere una capacità cubica aggiuntiva in verticale o in orizzontale. In alcuni Paesi, in particolare il Regno Unito, dove si trovano spazi per ponti e gallerie sulla rete stradale relativamente alti (principalmente per accogliere autobus a due piani), è possibile aumentare l’altezza del veicolo e inserire un doppio ponte per consentire il trasporto di due strati di pallet. Quello Britannico in realtà non ha limiti legali sull’altezza del veicolo, a causa dei vincoli dell’infrastruttura, cinque metri è generalmente considerato il massimo. Le aziende che trasportano prodotti a bassa densità possono trarre il massimo vantaggio dall’uso di due ponti, e per questo motivo ora sono ampiamente utilizzati dai principali rivenditori e vettori di pacchi nel Regno Unito (McKinnon e Campbell, 1997). Un grande rivenditore britannico ha dimostrato i vantaggi di double-decking (due ponti) confrontando i parametri operativi per le consegne utilizzando un veicolo a due piani e due veicoli a un piano con capacità simile. I costi di consegna unitaria, i km-veicolo e le emissioni di CO2 sono stati inferiori del 48% circa (DfT, 2005b).
Figura 3 Percentuale di chilometri per camion percorsi con peso e volume vincolati ai carichi
In gran parte del continente europeo vi è un limite di altezza di quattro metri, limitando strettamente, ma non eliminando, le opportunità di raddoppio (dei ponti). In altri Paesi Europei, come la Svezia, la Finlandia e i Paesi Bassi, le aziende hanno guadagnato il cubo extra “orizzontalmente” allungando il veicolo. Spesso questo aumento di lunghezza e numero di assi è stato accompagnato da un rilassamento del limite di peso massimo. Attualmente, all’interno dell’UE, la direttiva 96/53 / CE del Consiglio consente un veicolo di massimo 18,75 m di lunghezza per una combinazione di barra di traino e 16,5 m per veicoli con semirimorchio articolati. Rimorchi e semirimorchi conformi queste normative possono essere combinati con lunghezze complessive maggiori fino a 25,25m nel cosiddetto sistema modulare europeo. Tutti gli Stati membri dell’UE hanno il diritto di utilizzare questi veicoli più lunghi per uso domestico (vale a dire fino a quando non attraversano i confini internazionali né distorcono la concorrenza internazionale nel settore dei trasporti). Fino a poco tempo fa nessun paese dell’UE aveva presentato veicoli più lunghi e pesanti (LHV) a seguito della direttiva 96/53 /CE, sebbene l’uso di LHV in Svezia e in Finlandia sia precedente al loro ingresso nell’UE (McKinnon, 2008). Nel 2007, a seguito di un successo sul processo di percorso, il governo olandese ha deciso di autorizzare 25,25 metri di lunghezza del camion fino a un peso lordo massimo di 50 tonnellate (da quando alzato a 60 tonnellate). Gli studi sull’impatto ambientale ed economico degli LHV sono stati condotto anche in Germania (UBA, 2007), Belgio (Debauche eDecock, 2007), Svezia (Vierth et al, 2008) e Regno Unito (Knight et al, 2008). In parte alla luce di queste prove, i governi di entrambi i Paesi si sono rifiutati di legalizzare i veicoli da 25,25 metri, sebbene la Gran Bretagna stia prendendo in considerazione l’aumento della lunghezza massima dei veicoli articolati con un solo rimorchio da 16.5 a 18.75 metri. Un recente studio finanziato dall’UE ha concluso che gli LHV potrebbero essere ampiamente introdotti in Europa “senza nuocere la società Europea nel suo complesso “, sebbene abbia riconosciuto la necessità di numerose “contromisure” per ridurre al minimo l’impatto negativo su modalità alternative, attenuando i problemi di sicurezza e preparando l’infrastruttura stradale (trasporti e Mobility Leuven e altri, 2008). Organizzazioni di trasporto ferroviario di merci (ad es. UIC et al, 2007 e i gruppi ambientalisti (es. Federazione Europea dei trasporti e dell’ambiente, 2007) si oppongono con forza alla legalizzazione di quelli che chiamano “mega-camion”
Norme su salute sicurezza
Queste normative limitano l’altezza alla quale i carichi possono essere impilati su un veicolo per ridurre al minimo il rischio di lesioni agli agenti. Il raddoppio dei veicoli può aiutare a rilassare questo vincolo senza scendere a compromessi sulla sicurezza, sebbene solo laddove l’autorizzazione del veicolo lo permetta.
Limitazioni dell’orario di lavoro
Restrizioni legali sull’orario e il tempo di lavoro dei conducenti, che sono anche una forma di regolamentazione in materia di salute e sicurezza, può limitare la quantità di merci che possono essere raccolti e / o consegnate in un singolo turno. In particolare, loro possono ridurre la quantità di tempo disponibile per il backhauling e quindi aumentare la percentuale di funzionamento a vuoto. Si temeva che l’applicazione della direttiva sull’orario di lavoro alle operazioni di trasporto merci su strada europee nel 2006 avrebbe vanificato gli sforzi per migliorare il carico dei veicoli. In realtà, i governi europei hanno teso ad adottare un’interpretazione abbastanza liberale di “periodi di disponibilità” nei regolamenti WTD, dando agli operatori del veicolo maggiore flessibilità di quanto inizialmente previsto. Basato sull’esperienza del Regno Unito, il WTD sembra non aver avuto l’effetto negativo sull’utilizzo del veicolo previsto da alcuni commentatori.
Vincoli di capacità presso la sede dell’azienda
La dimensione di un ordine è spesso limitata dalla quantità di capacità di archiviazione disponibile al punto di consegna. In alcuni settori, questa capacità di archiviazione si è ristretta, in parte in linea con la pressione al ribasso sulle scorte ma anche per intensificare l’uso dello spazio. I rivenditori, ad esempio, hanno compresso le aree di magazzino nei loro negozi per massimizzare la superficie disponibile per esposizione e merchandising del prodotto. Dove le consegne sono ai magazzini, la dimensioni delle fessure nei sistemi di scaffalature può dettare l’altezza massima del pallet. In queste circostanze, le dimensioni e forme dei carichi unitari possono ottimizzare l’utilizzo dello spazio nel magazzino ma non nel veicolo di consegna (AT Kearney, 1997). In alcuni settori, come la chimica e l’agricoltura, la mancanza di investimenti ha impedito la capacità di serbatoi e silos di aumentare in linea con la portata del veicolo. L’espansione della loro capacità migliorerebbe l’utilizzo del veicolo e spesso produrrebbero un buon ritorno sugli investimenti. Dove le aziende hanno deliberatamente ridimensionato il loro spazio di archiviazione a spese di efficienza di trasporto, potrebbe essere necessario rivalutare i compromessi sui costi alla luce dell’aumento dei costi di trasporto e delle preoccupazioni ambientali.
Conclusione
Se tutti i camion avessero i lati di vetro la gente sarebbe sorpresa dalla quantità di aria che trasportano. Abbiamo analizzato le cause del sottoutilizzo della capacità del veicolo e le giustificazioni commerciali. Le aziende non possono permettersi di essere compiacenti, tuttavia, nel modo in cui gestiscono questa capacità. In risposta a una combinazione di pressioni economiche e ambientali, adesso stanno dando una maggiore priorità al riempimento del veicolo e cercando di più di superare i tradizionali vincoli sulla dimensione del carico e peso. Ciò richiede un riallineamento interno degli obiettivi aziendali all’interno delle aziende, nonché una maggiore collaborazione esterna attraverso e tra catene di approvvigionamento. Progressi nel veicolo, nella movimentazione dei materiali e la tecnologia dell’informazione possono aiutare gli sforzi a migliorare il caricamento, così come può farlo un investimento in più spazio di archiviazione nei punti critici della catena di approvvigionamento.
Anche il governo ha un ruolo da svolgere ottimizzando le dimensioni del veicolo e i limiti di peso per una distribuzione sostenibile, adottando meccanismi di tariffazione che incentivano un caricamento efficiente e un’esecuzione di programmi di buone pratiche per gli operatori del trasporto merci su strada. Un campione di 100 specialisti della logistica recentemente intervistati nel Regno Unito ha previsto che entro il 2020 la percentuale di chilometri di camion che cammineranno per strada vuoti scenderebbe del 19% e il peso medio del carico utile a carico sui viaggi aumenteranno del 12% (Piecyk e McKinnon, 2009). Questo conferma che esiste il potenziale per ottenere miglioramenti sostanziali nel caricamento del veicolo e possono essere raccolti i benefici economici e ambientali che ne conseguono.
Come le imprese affrontano la grande sfida alla green logistics? Su quale dei punti su esposti giocano maggiormente e su quali hanno intenzione di investire?
Ne discuteremo giorno 11 ottobre dalle ore 14.30 presso i locali del Palazzo della Cultura – Via Vittorio Emanuele 121 Catania, per ulteriori dettagli e partecipare clicca qui
Articolo tratto da Green Logistics: Improving the environmental sustainability of logistics. Edited by Alan MCKINNON, SHARON CULLINANE, MICHAEL BROWNE, ANTHONY WITHING. The Charted Institute of Logistics and Transport (UK)
Traduzione a cura di CentoCinquanta